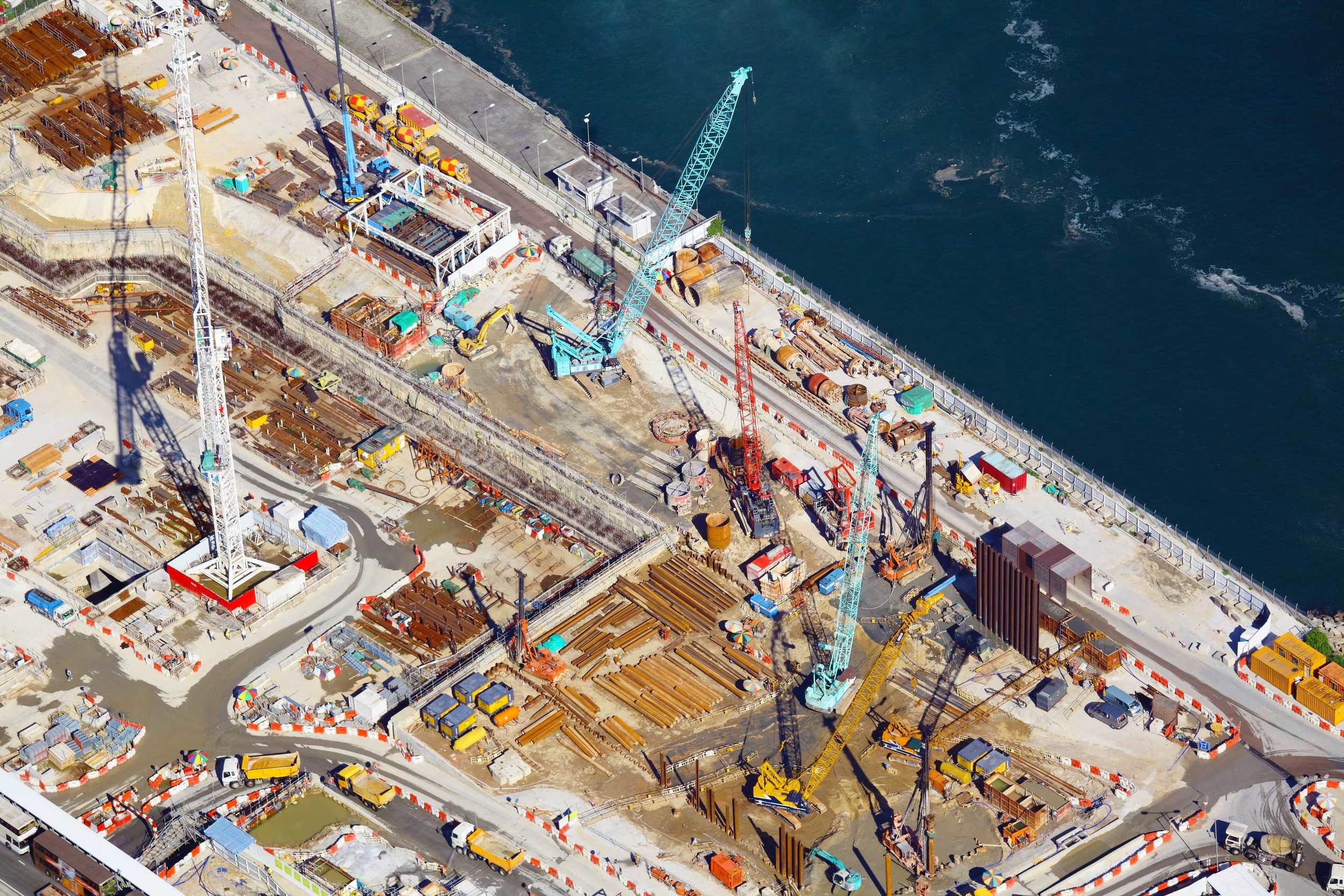
NOTES FROM THE FIELD
FLORIDA’S NEW BUILDING RECERTIFICATION LAW
Understanding Florida’s New Building Recertification Law: Key Impacts for Miami-Dade Hotels, Commercial Buildings, and Condos
Understanding Florida’s New Building Recertification Law: Key Impacts for Miami-Dade Hotels, Commercial Buildings, and Condos
Florida’s landscape is marked by its thriving tourism industry, bustling economy, and iconic skyline of hotels, commercial buildings, and high-rise condominiums. While these structures symbolize growth and prosperity, they also come with the critical responsibility of ensuring the safety and longevity of their occupants. To address this, Florida has implemented more stringent recertification requirements for buildings once they reach 30 years of age, covering all types of structures, including hotels and commercial properties.
At Kline Engineering, with over a decade of experience in structural safety inspections and complex repair projects across Florida, we understand property owners' challenges in navigating these new regulations. Our expert local team is here to guide you through the milestone inspection and recertification process, ensuring that your property meets all compliance requirements and remains safe for occupancy.
A Quick Recap of the Ordinance Rules
In May 2022, Florida enacted a new state law requiring milestone inspections for condominium and cooperative association buildings that are three stories or taller. This update significantly strengthens Miami-Dade County’s longstanding building recertification program, which has been in place since 1975 and was further revised on June 1, 2022, to align with state mandates.
Who Needs a Milestone Inspection?
1. Coastal Buildings and Recertification Deadlines:
Buildings constructed on or before 1982, already recertified under the 40-Year Program, will continue to follow their established schedule.
Buildings 30 years old by December 31, 2024, must undergo their first recertification inspection, with follow-ups every 10 years.
Buildings within three miles of the coastline and aged 25 by December 31, 2024, must also comply with inspections every 10 years thereafter.
2. Expanded Scope of Inspections:
The recertification process now requires a more comprehensive evaluation of structural and electrical systems, paying particular attention to vulnerable areas like underground parking garages, which are especially prone to issues in Miami-Dade’s coastal environment.
The Recertification Process
Under the new regulations, properties become subject to recertification every 30 years or every 25 years if the building is within 25 miles of a coastline, followed by a recertification every 10 years thereafter. Property owners receive a Notice of Required Recertification to start the process and must submit their recertification reports within 90 days of receiving the notice.
Specific residences, such as single-family homes, duplexes, and buildings with fewer than 10 occupants or less than 2,000 square feet, are exempt from this process.
Upon receiving the notice, property owners must hire a Florida-registered professional engineer or architect to conduct a thorough inspection and certify that the building is structurally and electrically safe for continued occupancy. This professional must have proven qualifications in the relevant technical field related to the inspection.
What Property Owners Should Know
The new regulations underscore the importance of proactive maintenance and early intervention. For property owners, particularly those managing older or coastal buildings, it’s crucial to prioritize these inspections to avoid fines and, more importantly, to ensure the safety of your occupants. The December 31, 2024, deadline is crucial for those managing coastal properties built between 1983 and 1997.
Proactive maintenance not only helps you meet these new legal requirements but also preserves property value and ensures the safety and well-being of residents. Well-maintained buildings will typically find the recertification process straightforward, while those with deferred maintenance may face significant challenges in terms of time and financial investment.
The Scope of Recertification Inspections
Recertification inspections encompass a wide range of critical building components, including:
Structural Integrity: Foundation, masonry bearing walls, main structural elements (columns, beams, slabs), wall, floor, roof framing systems, and the building façade.
Electrical Systems: Comprehensive assessment to ensure compliance with safety standards.
Fire Safety Measures, Accessibility Standards, and Parking Lot Safety are essential to ensuring buildings remain functional, safe, and resilient in Florida’s challenging environment.
These inspections are crucial for identifying deficiencies and recommending corrective actions to address potential hazards.
The Two-Phase Milestone Inspection Process
Phase One Inspection:
A licensed architect or engineer visually examines the building’s habitable and non-habitable areas to assess its structural condition. A Phase Two inspection is unnecessary if no significant structural deterioration is detected and the inspection report is submitted.
Phase Two Inspection:
A more detailed Phase Two inspection is required if substantial structural deterioration is identified in Phase One. This may involve both destructive and non-destructive testing to assess the issues thoroughly, confirm the building’s structural integrity, and recommend necessary repairs. An inspection report is submitted after the completion of this phase.
Who Can Perform a Recertification Inspection?
Buildings 3 stories or less (or under 50 feet): Can be inspected by any Florida licensed architect or Structural engineer.
Buildings 4 stories or taller (or threshold buildings): Must be inspected by a Florida licensed structural engineer and electrical engineer required for the electrical system.
Partner with Kline Engineering
Navigating Florida’s new building recertification law requires expertise and diligence. At Kline Engineering, we guide you through every step of the structural integrity milestone inspection process, ensuring your property remains compliant and safe. Whether you manage a hotel, commercial building, or high-rise condominium, our team of seasoned professionals is ready to provide the guidance and support you need.
For more detailed information on Miami-Dade’s recertification program or to schedule an inspection, contact Kline Engineering today. Let’s work together to keep your property safe, compliant, and secure.
GRIETAS EN LAS CUÑAS DE TENSAR POSTENSADAS: ¿ES ESTO UN PROBLEMA?
Written by KLINE senior project engineer, Joseph Dubois and translated by KLINE Senior Project Engineer, Sergio Fagundo
¿Hemos escuchado que las grietas son siempre malas noticias, cierto? Las fisuras en general pueden reducir el atractivo estético, así como la integridad estructural de cualquier elemento que haya sido agrietada. Pero, el verdadero problema con las grietas es que son casi imposibles de evitar, lo que plantea la pregunta: ¿qué grietas están bien y cuáles son inaceptables? El postensado (PT) no escapa a esta cuestión, por lo que abordaremos el siguiente dilema:
La situación
Diseño de las cuñas para el concreto postensado.
Entender a diferenciar entre las grietas aceptables e inaceptables
¡Empecemos entendiendo que son las cuñas!
Es una tarde soleada y el trabajo de hoy es tensar los cables del primer piso garantizando no solo que se cumpla la fuerza especificada de postensado, sino la instalación de las cuñas de forma correcta. Usted sabe que ambos factores son críticos para la integridad estructural del edificio, por lo que empieza verificando cuidadosamente el medidor: 7000 libras por pies cuadrado: ¡Listo! A continuación, retira el gato hidráulico e inspecciona las cuñas. Las cuñas están completamente asentadas en el anclaje y el tendón está firmemente conectado, pero un momento… ¡hay una pequeña grieta en la cuña izquierda! La grieta parece tan pequeña que no te preocupa demasiado, pero nunca has visto esto antes y quieres asegurarte de que la conexión sea buena.
Propósito y fabricación de la cuña postensada
Para abordar adecuadamente el escenario anterior, debemos entender el propósito específico de las cuñas para cables postensados, junto con su fabricación. Una cuña es uno de los materiales para los sistemas de postensado encargado de fijar el cable al anclaje después de tensar el cable. El objetivo final de las cuñas PT es anclar de forma segura los tendones postensados al hormigón circundante (a través del anclaje) y mantener la fuerza de tensión durante toda la vida útil del edificio. Esto requiere que las cuñas PT sean fuertes y duraderas. A diferencia de las cuñas de pretensado, las cuñas de postensado son de un solo uso. Al igual que la trompeta y la placa activa, es un elemento fundamental en un anclaje postensado.
El Manual de instalación de tendones de postensado de la Administración Federal de Carreteras de Estados Unidos (“The Federal Highway Administration Post-Tensioning Tendon Installation and Grouting Manual - FHWA NHI 13.026, en inglés) establece que todas las cuñas PT deben tener "dentado interior para sujetar el cable de tensión", y estar hechas de "aAleación de acero altamente resistente o acero de bajo carbono". “La razón para requerir una carcasa endurecida es garantizar que los dientes de la cuña sujeten o “muerdan” firmemente el tendón sin deformarlo ni permitir que el tendón se deslice. Observe que sólo el exterior de la cuña está endurecido; esto se debe a que la cuña debe tener un “núcleo dúctil, para poder… ajustarse a la irregularidad entre el cable y el orificio cónico de la cuña” (FHWA-NHI-13-026). En resumen, las cuñas PT tienen un interior blando para adaptarse entre superficies irregulares y un exterior duro con dientes de agarre para retener la fuerza en los tendones postensados.
Entonces, ¿MITO O REALIDAD?
Conociendo para qué están diseñadas las cuñas PT y cómo se fabrican, echemos otro vistazo a la grieta que encontró. Hay tres razones principales por las que una cuña de PT podría agrietarse: primero, la superficie del tendón es irregular, lo que obliga a la cuña a doblarse y ajustarse cuando se tensiona el cable. En segundo lugar, endurecer el acero en la caja de la cuña hace que el acero se vuelva frágil. y, en tercer lugar, la cuña está defectuosa o dañada.
Debido a la necesidad de deformación para permitir que la cuña “muerda” adecuadamente el cable postensado, las primeras dos razones enumeradas no son razón de preocupación cuando la grieta está limitada a la superficie del concreto. Esto lo afirma el Manual de Campo para Cables Postensado “PTI’s Field Installation Manual for Unbonded Single Strand Tendons (PTIM10.3-00) en Ingles, que establece que “pueden aparecer grietas finas en la superficie cementada de las cuñas…” y que esto “…no afectan la integridad estructural del sistema de postensado.” Sin embargo, lo que no es aceptable es que el núcleo dúctil de la cuña también se agriete, rompiendo la cuña en múltiples pedazos (FHWA-NHI-13-026). Esto puede deberse tanto a defectos del fabricante como a errores de instalación, así como a cuñas asentadas de manera desigual, cuñas muy corroídas, cuñas y/o anclajes torcidos y gatos tensores colocados incorrectamente. Adicional, no es aceptable cuando las cuñas presenten grietas continuas y puntas parcialmente desprendidas a causa de las fisuras o cuando las grietas son horizontales o inclinadas. Para evitar problemas y grietas inaceptables, hay que asegurar que todas las cuñas estén en buena condición con base al criterio del PTI (“Instituto del Postensado”) antes de su instalación.
Entonces, no todas las grietas observadas son malas. Ahora, usted sabe determinar la diferencia! Las cuñas completamente agrietadas son un peligro y deben considerarse defectuosas, sin embargo, hay que recordar que las cuñas con grietas en la superficie radial son estructuralmente sólidas. Los tendones de postensado se diseñan e instalan con un nivel específico de esfuerzo en mente. Incluso con fisuras menores, los tendones pueden seguir manteniendo el esfuerzo deseado, asegurando que la capacidad estructural no se vea comprometida.
Como regla general, las micro fisuras radiales no deberían afectar el funcionamiento de la cuña. Mientras los cables no se deslicen, no es necesario volver a acuñarlos. Sin embargo, es importante destacar que, aunque las fisuras menores en las cuñas postensadas generalmente no son una preocupación estructural, no deben ser ignoradas. Inspecciones regulares y un mantenimiento adecuado son fundamentales para garantizar la durabilidad y seguridad a largo plazo de las estructuras postensadas. Si las fisuras se dejan sin atención y se les permite propagarse ampliamente, podrían potencialmente llevar a problemas estructurales más significativos con el tiempo.
Si es contratista o inspector, es esencial compartir esta información con su equipo y colegas para disipar el mito que rodea las grietas en las cuñas postensadas. Si tiene otras preguntas o inquietudes sobre el postensado, consulte nuestro blog sobre los "Top 10 Common Post-Tensioning Myths Debunked," (próximamente en español) y no dude en comunicarse con nosotros para obtener asesoramiento y asistencia de expertos.
CRACKS IN PT WEDGES: IS THIS AN ISSUE?
In this blog, we delve into the issue of cracks in PT wedges and differentiate between acceptable and unacceptable cracks. We explore the purpose and construction of PT wedges, highlighting their importance in securely anchoring tendons to concrete structures. We debunk the myth that all cracks are bad by explaining the reasons behind PT wedge cracking, including irregular tendon surfaces, brittle steel, and defects.
Written by KLINE Senior Project Engineer, Joseph Dubois
Cracks are always a bad thing, right? They reduce both the aesthetic appeal and the structural integrity of whatever has been cracked. The problem is that cracks are nearly impossible to avoid, which begs the question: Which cracks are okay and which cracks are unacceptable? Post-tensioning (PT) does not escape this question, so we will address the following:
The Situation
Post-tensioning Wedge Design
Understanding Acceptable vs Unacceptable PT Wedge Cracks
Setting the Stage, er, Wedge!
It is a sunny afternoon and today’s task is stressing the tendons of the first floor, ensuring the specified force is met along with setting the wedges properly. You know both of these factors are critical to the structural integrity of the building, so you carefully check the gauge – 7,000 psi: check! Next, you remove the jack and inspect the wedges. The wedges are fully seated in the anchor and the tendon is securely gripped, but wait, there is a hairline crack on the left wedge! The crack seems so small that you are not too concerned, but you have never seen this before and want to make sure the connection is sound.
PT Wedge Purpose and Construction
To properly address the scenario above, we must take a look at the specific purpose of PT wedges, along with their construction. The ultimate goal of PT wedges is to securely anchor post-tensioned tendons/strands to the surrounding concrete (through the anchorage), and maintain the tension force throughout the life of the building. This requires PT wedges to be strong and durable. The Federal Highway Administration Post-Tensioning Tendon Installation and Grouting Manual (FHWA-NHI-13-026) states that all PT wedges must have “internal serrated teeth for gripping the strand,” be made of “case-hardened low carbon or alloy steel.” The reason for requiring a hardened case is to ensure that the serrated teeth firmly grip the tendon without deforming or allowing the tendon to slip. Notice that only the outer “case” of the PT wedge is hardened; this is because the wedge must have a “ductile core, in order to … conform to the irregularity between the strand and wedge hole” (FHWA-NHI-13-026). To summarize, PT wedges have a soft interior to conform between irregular surfaces and a hard exterior with gripping teeth to retain the force in PT tendons.
Myth or Truth?
Knowing what PT wedges are designed for and how they are constructed, let us take another look at the crack you found. There are three main reasons why a PT wedge might crack: First, the tendon surface is irregular which forces the wedge to bend and conform when the tendon is stressed. Second, hardening the steel in the wedge case makes the steel brittle. Third, the wedge is defective or damaged. Due to the need for deformation to enable the wedge to properly grip the PT strand, the first two reasons for cracking are not a concern when the crack is limited to the surface. This is affirmed by PTI’s Field Manual for Unbonded Single Strand Tendons (PTI M10.3-00) which states that “hairline cracks may appear in the case-hardened surface of wedges …” and that they “… do not affect the integrity of the post-tensioning system.” However, what is not acceptable is if the ductile core of the wedge also cracks, breaking the wedge into multiple pieces (FHWA-NHI-13-026). This can happen both from manufacturer defects and from installation errors, such as unevenly seated wedges, highly corroded wedges, skewed wedges and/or anchors, and improperly placed stressing jacks. Not acceptable are wedges that have been broken into pieces signifying not only hard surfaces but also brittle cores. Horizontal or inclined breaks are also considered unacceptable.
So most cracks observed in PT wedges are not bad, and now you know how to tell the difference! Wedges cracked completely through should be considered defective, but wedges with radial surface cracks are structurally sound.
In general, radial micro cracks should not affect the wedge capability. As long as the strands are not slipping, Re-wedging is not necessary.
If you are a contractor or inspector, it is essential to share this information with your team and colleagues to dispel the myth surrounding cracks in post-tensioned wedges. If you have other questions or concerns about post-tensioning, check out our blog on the "Top 10 Common Post-Tensioning Myths Debunked," and do not hesitate to reach out to us for expert advice and assistance.
UNLEASH THE POWER OF TECHNOLOGY
Groundbreaking advancements in wireless embedded sensor technology, IoT data transmission, analysis, and AI-powered predictive analytics, have transformed the way we monitor and ensure the integrity of new and existing structures like never before.
In this blog, you will explore the state of the art in this field, how IoT facilitates seamless data collection and analysis; and AI algorithms analyze historical data to predict future structural degradation, empowering property owners to make informed decisions promptly.
In today's rapidly evolving built environment, ensuring the safety, durability, sustainability, and resilience of our infrastructure is of utmost importance. One of the major challenges faced by structural and facilities engineers is its detection and we will explore the current state of the art in this field, highlighting the capabilities of wireless sensors, data collection, and analysis methodologies, and the role of AI in predicting future structural degradation.
CURRENT STATE OF THE ART IN STRUCTURAL HEALTH MONITORING:
Traditionally, structural health monitoring relied on periodic visual inspections and manual measurements, which were time-consuming, limited in scope, and prone to human error. However, the advent of wireless embedded sensor technology has revolutionized the field. These sensors can be installed during construction or in rehabilitation and repair projects, enabling continuous monitoring of critical parameters such as temperature, humidity, strain, cracks, and corrosion. They provide continuous real-time data on the behavior of a structure, enabling engineers and owners to identify issues before they escalate into significant structural degradation. When caught early, potential issues can be corrected or mitigated.
When corrosion is allowed to progress to a state that is detectable by visual inspection, the costs to repair the structure can be an order of magnitude greater. The figure indicates how repair costs increase exponentially with the progression of corrosion.
WIRELESS DATA TRANSMISSION:
Wireless sensor technology is available today that can be installed during original construction or during a repair or rehabilitation project. RFID enables wireless communication between the embedded sensors and the data reader (gateway). The sensors can be read remotely, eliminating the need for physical access to each sensor.
Gateways can be permanently fixed to the structure, or they can be handheld devices used by the structural engineer during inspections. With fixed gateways, data collection is continuous and automated and does not rely on manual inspections. Embedded sensors require no batteries, so they will last over 80 years in the structure.
DATA COLLECTION IN THE IOT:
The Internet of Things (IoT) plays a pivotal role in enabling seamless data collection from a vast network of wireless sensors. These sensors are interconnected and transmit their data to a central database via wireless networks. This centralized data collection allows for real-time monitoring and analysis, empowering structural engineers to make informed decisions promptly. The IoT infrastructure also facilitates data aggregation, ensuring a comprehensive overview of the structural health across multiple locations and time frames.
Figure 3. Fixed data collection gateway
DATA ANALYSIS:
Figure 4. Handheld data collection gateway
The enormous amount of data collected from wireless sensors necessitates advanced data analysis techniques. Data analysis algorithms, such as machine learning and statistical modeling, can identify patterns and correlations within the sensor data. By employing anomaly detection algorithms, engineers can pinpoint structural hotspots where corrosion is occurring. Additionally, data analysis can provide valuable insights into the environmental conditions that contribute to corrosion such as moisture intrusion, aiding in the development of targeted preventive measures.
USING AI TO PREDICT FUTURE STRUCTURAL DEGRADATION:
Artificial intelligence (AI) algorithms can analyze historical sensor data, environmental factors, and other relevant parameters to predict future structural degradation. By training AI models on a vast dataset of structural health information, the system can learn patterns and indicators that precede corrosion-related issues. AI-powered predictive analytics can alert engineers to potential problems well in advance, enabling proactive maintenance and cost-effective interventions.
CORRODEC 2G BY INFRASTRUCTURETEK:
One notable product in the field of wireless embedded sensor technology is CorroDec 2G, by InfrastructureTek in partnership with Infrasolute. CorroDec 2G is an advanced wireless sensor system specifically designed for continuous monitoring of corrosion in reinforced concrete structures. It provides real-time corrosion detection (not corrosion potential), allowing engineers to assess the rate and severity of corrosion accurately. The system's compatibility with RFID technology ensures seamless data transmission, collection, and analysis. Furthermore, the long lifespan of CorroDec 2G sensors, lasting over 70 years within a structure, ensures long-term monitoring capabilities, saving costs for the structure's owner and contributing to a safer and more durable structure over its lifetime.
Wireless embedded sensor technology, combined with RFID data transmission, IoT data collection, data analysis, and AI-powered predictive analytics, has transformed the field of structural health monitoring. This technology enables continuous, long-term monitoring of buildings susceptible to corrosion-induced deterioration, whether in new construction or rehabilitation projects. By employing products like CorroDec 2G, structural engineers can proactively manage corrosion-related risks, save costs on repairs, and ensure the safety and longevity of structures for years to come.
REFRESH AND REPAIR: WATERGATE SOUTH CO-OP BOARD TACKLES BALCONIES
Anatomy of the Watergate’s balconies repair project. Go behind the scenes of our almost 3-year repair plan to ensure the safety and durability of the balconies of one of DC’s most iconic landmarks.
The Watergate is a historic apartment complex with three luxury residential buildings located on the edge of Northwest Washington, DC.
Watergate South co-op building accounts for 257 luxury residences overlooking the Potomac River across its 14 stories. The Watergate complex's wraparound balconies and curving towers are one of its most distinctive features, some balconies extend as far as 129 feet providing panoramic views of the surrounding landmarks.
Since 2011, Kline Engineering has been retained by Watergate South as their structural engineering consultant on several projects. For one of our most recently finished ones, our team inspected every balcony on the 14-story Watergate South Building.
by Joseph DuBoisTHE PROJECT
As a rule, the Watergate South board and management prioritize a safe and pleasant environment for all its residents. Due to the natural deterioration of the building façade and balconies, Kline Engineering & Consulting (KLINE) was brought on to perform a comprehensive inspection as a part of Watergate South’s maintenance plan. Being experts in Post-Tensioning (PT), KLINE is aptly suited to evaluate structures such as this innovative PT complex built in 1971.
Inspection Results
This visual, non-invasive inspection was performed in May of 2019, covering both the structural and aesthetic conditions of the balconies. We gently sounded the concrete slabs and balustrades with hammers, searching for spalled or delaminated concrete. The balcony handrails and guardrails are secured to the concrete with anchor bolts – areas where cracking often occurs. Several of the unique concrete balustrades had cracked, allowing water to corrode the metal reinforcing bars inside, causing small chunks of concrete to come loose. KLINE also recorded signs of leaks or ponding of water to determine the condition of the drainage system. The more vulnerable areas higher in the building generally showed higher levels of deterioration than the lower areas.
At the same time, notes were taken on the state of the paint covering the slabs, railings, and façade frames. Though not structural, these coatings provide necessary protection to the concrete and metal substrates beneath. We then focused on the remaining features including balcony dividers and windows.
KLINE Senior Project Engineer Joseph DuBois records balcony structural and aesthetic conditions.
MOVING FORWARD
After facing many challenges due to the pandemic, Watergate South decided to move forward with the project and KLINE performed a follow-up inspection in March of 2022. This encompassed reviewing balconies with critical repairs and inspecting any that were not accessible in 2019. This enabled KLINE to determine the progression of deterioration between 2019 and 2022, which gave valuable insight into the necessity of the repairs.
With the findings of these two inspections, KLINE designed repairs for every single balcony, ranging from purely aesthetic and preventative to localized structural and drainage rehabilitation. A challenge in this repair design is preserving the historic appearance of the building for which mockup assemblies were mandated during the initial repair phase. This allows Watergate South to know exactly what the repairs will look like before commencing with the repairs on the entire building.
To minimize both time and cost – while prioritizing quality – KLINE conducted a competitive bidding process with reputable contractors in the area, most already familiar with the site. This gives the board and management the best possible outcome for this project.
Precast Balustrade Concrete Spall and Corrosion
Coating Deterioration of Concrete Slab Soffit
CONCLUSION
Over 50 years old, this iconic building with the then-innovative Post-Tensioned concrete design has stood the test of time. The board and management’s decision to proactively maintain the façade and balconies ensure the safety of the residents and the building’s structural integrity. With these repairs, Watergate South will continue to be a coveted residence for many years to come.
Joseph DuBois is a Senior Project Engineer on Kline Engineering & Consulting’s Team.
6 UNEXPECTED ADVANTAGES OF POST-TENSIONING EVERY ARCHITECT SHOULD KNOW
Post-tensioning is not only kind to the environment, but it also reduces construction time, material, and costs. In our latest blog post, we discussed six of the unexpected advantages of using post-tensioning in your next building project.
Post-tensioned concrete construction in buildings has seen extraordinary growth in North America since it was first introduced in the 1950’s. By some estimates, more than 60,000 post-tensioned concrete buildings have been built in the United States covering upwards of 6 billion ft2 of floor area.1,2 Prestressed concrete and, more specifically, post-tensioned concrete is perhaps the most significant development in the design and construction of concrete buildings over the past century.
Most structural engineers and architects are familiar with the commonly known benefits of post-tensioned concrete, such as allowing for thinner members, longer spans, reduced deflections, and reduced costs. These benefits are well established, but did you know that post-tensioned concrete results in a more sustainable design solution when compared to other types of construction? This article looks at 6 of the “unexpected” benefits of using post-tensioning for building construction.
Unexpected Benefits of Choosing Post-Tensioning in Building Projects:
1. Cost-Savings +++
Most of us know that post-tensioning saves construction costs in terms of concrete and reinforcing steel quantities when compared to conventional reinforced concrete construction. It may surprise some to learn of the cascading cost savings that occur in many components of the total building cost. Below is a listing of building components that will experience cost savings when compared to any other building construction type:
Since PT floors are thinner, there is generally an overall savings of 20% in the dead load of the building compared to conventional concrete. Due to this decrease in dead load, the amount of reinforcing steel is reduced in columns and foundations.
When seismic effects govern the lateral load resisting systems, the cost of shear walls and foundations can be reduced by 20% or more due to the reduced structural mass.
Since PT floors are thinner than conventional concrete floors and significantly thinner than composite concrete over metal deck systems, floor-to-floor heights are reduced. The typical structural depth for a steel office building floor is 30 inches. Similarly, the typical structural depth for a conventional concrete office building floor is 24 – 26 inches. The structural depth for a post-tensioned concrete office floor is 18 inches or less. This saves more than 6 inches per floor compared to a conventional concrete building, and over 1 foot per floor compared to a steel building. Therefore, the costs for all building systems tied to building height are reduced proportional to the reduction in building height. For example, the cost of the building façade will be reduced by 8 percent compared to a structural steel office building. These savings also apply to MEP risers, elevators, and more.
2. Swift Construction
Another benefit of post-tensioning is speedy construction. The reduction in materials used and the simplicity of the formwork ensure that construction of a floor can be completed faster. Post-tensioning saves you time in these areas:
Using less steel.
One of the most time-consuming activities in construction is placing steel, and since PT designs reduce the quantity of steel needed, slabs will be ready to pour at an earlier date. Unlike conventional concrete slabs, which requires approximately 5 to 7 lb./ft2 of steel, post-tensioned flat slabs only need about 2 to 3 lb./ft2 of steel.
Slab formwork and reshoring can be removed earlier.
PT slabs are ready for stressing once the concrete reaches a strength of 3000 psi. It is quite common to stress the tendons 2 to 3 days after the pour. Once stressing is complete, formwork can be stripped immediately and moved to a subsequent pour.
Follow-on trades can start sooner.
Thinner slabs and beams require fewer levels of reshoring below the formwork. This allows follow-on trades such as construction of interior partitions, façade work, and MEP to start their work earlier. This significantly reduces the overall project schedule.
3. Reduced Floor Vibration and Sag
Construction of lighter and longer floor structures can result in increased incidences of vibration and deflection. However, post-tensioning produces two key characteristics in the concrete that significantly reduce vibration and sag. First, the profile of the cables within the concrete produce a load balancing effect. Load balancing from post-tensioning effectively carries a significant portion of the slab weight so that the concrete slab does not feel its own weight. This results in reduced deflections or sag. Second, the slabs are designed to remain uncracked under normal loading. When slabs remain uncracked, they have a much higher stiffness. In technical terms, we are able to use the “gross section properties” in the calculation of deflection and vibrations. For non-prestressed slabs, we must use the “cracked transformed section properties” in these calculations.
4. Architectural Flexibility with Space and Form
Conventional concrete slabs require a specific level of thickness to maintain their strength and serviceability. However, with post-tensioned concrete, you can build thinner and longer slabs without compromising structural serviceability and strength. The fewer columns give greater flexibility in floor plans and layouts, especially in office and residential buildings.
PT allows you to design longer unsupported spans that are strong with thinner floors. This makes post-tensioning an ideal technique for creating concrete slabs for expansive structures such as parking garages, auditoriums, roofs, bridges, and customized architectural designs.
Since post-tensioned concrete can be profiled for longer spans, curved floors, and irregular grids, it is ideal for creating extended cantilevered slabs for exquisitely designed balconies and other futuristic architectural features. Post-tensioned slabs can create sleek and exceptional designs since they give way to dynamic and alluring contours. They allow architects and engineers to express creativity in building plans without compromising quality, strength, and stability. In simple terms, PT concrete elements deliver outstanding and efficient architectural features, offering infinite possibilities for structural designs. PT flat plates with unbonded tendons allow for random placement of columns supporting the floor slab. This provides tremendous flexibility for architectural designs.
5. Strength and Flexibility with Building Foundations
Post-tensioning can be used in mat foundations offering many benefits to the project. Costs will be reduced due to a reduction in the depth of the foundation system. This will offer savings in materials such as concrete and rebar. Additionally, costs for foundation excavation and support of excavation will be reduced as well.
The prestressing forces and cable profiles in mat foundations provide the ability to actively transfer loads within the foundation system. This gives post-tensioned foundations the unique ability to span over subsurface weak points such as utilities, tunnels, stormwater management vaults, etc. Post-tensioning can also be specifically designed to balance loading going to supporting piles or caissons by moving loads from one group of piles to another.
Expansive clay soils or soft soils can wreak havoc on structures that are built using conventional concrete. However, post-tensioned concrete boasts high-end structural advantages, such as high stability and minimum differential settlement, making it ideal for building foundations with soft or expansive clay soils.
6. Sustainability
Using post-tensioned concrete significantly reduces concrete and steel quantities in the structure when compared to conventional concrete or steel with composite floor slab construction. This efficiency has a cascading benefit throughout the structure by reducing the overall self-weight of the floors transferred to columns, shear walls, and foundations. Reduction in concrete materials reduce cement consumption which is a contributor to greenhouse gas emissions. As stated earlier, there are reductions in other building components as well, including building façade, MEP, mechanical equipment, and elevators. Thus, the environmental impact is minimized throughout the life cycle of the building through diminished material consumption, faster construction, fewer transportation trips, and fewer disruptions to the local neighborhood during construction. Moreover, due to reduced overall building height, there is a reduction in the volume of interior conditioned space. And since concrete provides superior thermal mass, the costs for heating and cooling will be diminished throughout the life of the building.
Post-tensioned concrete construction is a major contributor to the overall sustainability of the building. Architects, engineers, and owners will reap tremendous long-term benefits in sustainability and resiliency through the use of post-tensioned concrete.
If you need a post-tensioning expert or have any questions as you prepare for your next building project, talk to us.
References
1. Bondy, K.B., “The State of Post-Tensioned Concrete Education”, Concrete International, October 2014, pp 32-36
2. Post-Tensioning Institute, “Tonnage Report”, PTI, 2020
If you need a post-tensioning expert or have any questions as you prepare for your next building project, consult an expert!
Photo credit “The Surf Club Four Seasons Residences” to miamiluxuryhomes.com
TOP 6 STAGE STRESSING QUESTIONS ANSWERED!
Stressing about Stage Stressing? No need.
Please check our blog post where we answered some of the most common FAQ’s contractors may have while dealing with stage stressing.
WRITTEN BY KLINE ASSOCIATE ENGINEER, KATHERINE FARLEY, P.E.
Post-tensioning (PT) is widely used in large supporting elements such as transfer girders, transfer slabs, and mat foundations. While the advantages of PT are widely known for typical building construction, PT is particularly well suited for the design of transfer elements in buildings. PT transfer girders, for example, will typically be small in comparison to steel or non-prestressed concrete girders. Moreover, the active PT force will counteract gravity loads to reduce long-term deflections. The design of these members can be challenging due to the large PT force concentration required to pick up several levels above. The effects of applying this magnitude of PT force at once can cause several issues, including massive cracks and blow-outs. For this reason, stage stressing becomes a crucial design step. The engineer of record (EOR) should determine if stage stressing is required, and if required, the EOR should be the one to specify all stage stressing requirements.
Below is a list of common FAQ’s contractors may have while dealing with stage stressing:
Q1. How do I know if stage stressing is required?
Stage stressing requirements should be provided in the structural drawings. However, it is not uncommon for the EOR to delegate this responsibility to the PT supplier, or in some cases to ignore them altogether. If the project has PT transfer girders, transfer slabs, podium slabs, or a mat foundation, stage stressing may be required. If the drawings are silent regarding stage stressing, it is appropriate to contact the EOR through an RFI.
To dive into the nitty-gritties, the first indicator that stage stressing is required are initial concrete compressive stresses larger than 0.60f’ci. When an engineer recognizes initial compressive stresses are an issue, there are only a couple ways to reduce these stresses. Either reduce the PT force or increase the initial compressive strength of the member. The second option is often not feasible because the required initial concrete strength would be unachievable given a tight construction schedule. Therefore, reducing the amount of PT initially applied to the member through stage stressing is the preferred option.
Q2. Do I need shoring during any part of the stage stressing operation?
If stage stressing is designed properly, no shoring of the transfer element is required after the initial stage stressing sequence is complete and stressing records are approved by the EOR. Once the initial PT force is applied, the member gains enough structural capacity to support its own self-weight, plus additional loading from the levels above. The engineer should design the stage stressing sequence in a way that eliminates post-initial stage shoring.
Q3. Is camber required during stage stressing?
No. However, deflection at early stages of stressing can be an issue in many cases. The engineer may request cambering to compensate for any large short-term deflection occurring during stage stressing. When requesting camber, the engineer should pay special attention to the interaction of adding PT at different stages and the long-term effects. Understanding this will eliminate deflection issues that can impact third party work, such as façade and window installation.
Q4. How is the number of stages determined?
The number of stages is determined by the engineer based on the required PT force together with the number of levels supported by the transfer element. Based on practical experience, a good indicator of the number of stressing stages for a structural element is the ratio between the actual initial tensile stress and 6√f’ci.
For instance, if a transfer slab supporting 6 levels above has an initial stress of 12√f’ci, then:
Q5. For bonded PT transfer girders, does it matter which tendons are stressed first?
Yes. The arrangement of bonded PT tendons within a girder is driven by the center of gravity of the strands (CGS) at the anchorage relative to the center of gravity of the concrete (CGC). In cases where multiple tendons are required, the anchorages will most likely be arranged in rows. As PT force is applied at each stage, the engineer should verify that the CGS of every stage is within the kern (middle third) of the section in both the vertical and horizontal directions.
Q6. Can I partially stress a tendon in any given stage?
No. It is recommended that tendons (bonded and unbonded) be stressed to their full jacking force in one stage. For this reason, the size and arrangement of stressing anchorages must be coordinated with the stage stressing requirements in order to ensure that the PT force and CGS at each stage are acceptable to the EOR. Stressing a tendon multiple times to achieve the jacking force can result in damaged or broken strands. Such a procedure can also lead to unsafe practices.
Post-tensioning is a powerful method for the design of transfer elements, not only because of the advantages mentioned above but also because the engineer is able to fine-tune forces and stresses within the members. Though the answers to the above FAQs apply to most situations for typical projects, every job is unique. Therefore, it is vital that an experienced PT designer who understands the behavior of transfer elements with the applied loading be engaged to design the members and specify the required stage stressing.
If you need a post-tensioning expert or have any questions as you prepare for your next building project, consult an expert!
TOP 10 COMMON POST-TENSIONING MYTHS DEBUNKED
Whether you are an architect seeking the best way to design a space or an engineer who is relatively new to post-tensioning, this post will shed light on the top 10 false assumptions about post-tensioned structures and uncover the truth.
WRITTEN BY KLINE PRESIDENT, DON KLINE
Post-tensioned concrete has been used in building construction since the late 1950’s. Today post-tensioning is becoming increasingly popular for many different use categories including parking structures, high-rise office and residential, hospitality, and podium slabs for mixed-use projects. (To find out more on podiums, check out everything you need to know about building with concrete podium slabs). Whether you are an architect seeking the best way to design a space or an engineer who is relatively new to post-tensioning, this post will shed light on the top 10 false assumptions about post-tensioned structures and uncover the truth.
1. Myth: It’s difficult to core holes or cut future openings in post-tensioned slabs.
Reality: Post-Tensioned structures can be modified just like any other building construction method as long as future modification is considered in the initial design. Tendon layouts can be designed to allow for future cores, knockouts, and openings. A 2-way banded layout can be employed to leave huge areas for future openings. Designers of office buildings, hospitals, and other medical facilities are often reticent to use post-tensioning because of this misconception. This is unfortunate because these buildings would benefit most from the cost efficiencies inherent in post-tensioned structures (see Myth 9). Planning and collaboration between the architect and the engineer will result in a smart, flexible design solution.
2. Myth: Post-tensioned parking garages are more expensive than precast parking garages.
Reality: It’s important to remember that the overall budget of a structure is more than just the initial construction cost. While upfront costs for a post-tensioned parking structure can be higher than for precast, maintenance and repair costs are considerably lower. Over the life cycle of the building, precast is often the more expensive approach. If durability, minimal maintenance, an open layout, reduced vibration, and better distribution of light in the structure are of the highest priority, post-tensioning is truly the superior building choice.
3. Myth: You need sophisticated finite element analysis software to design post-tensioned structures.
Reality: Finite element (FE) software is used to provide structural analysis to design buildings with complex geometries. When the user doesn’t fully understand the limitations of the program or if they are inexperienced in post-tensioning, the FE program will likely deliver weak or incorrect designs. PT structures can be designed by hand although this is very time-consuming and impractical. Although FE design programs can be a powerful tool, most buildings can be simplified into 2-D strip models that are easily designed using common equivalent frame design software. And in our experience, using 2-D frame software usually results in the more efficient and safe designs.
4. Myth: General zone reinforcement should be designed by the post-tensioning supplier.
Reality: This is actually the responsibility of the engineer of record. The American Concrete Institute’s building code requirements for structural concrete (ACI 318) describes the anchorage zone as 2 distinct zones: local zone and general zone. ACI 318 requires that the contract documents assign responsibility for the design of these 2 zones. The local zone is the prism immediately surrounding the anchorage device and the design of this zone is strongly influenced by the characteristics of the anchorage device. It follows that the design of the local zone should be performed by the post-tensioning supplier. The general zone encompasses a larger zone around the local zone and is inclusive of the local zone. The design of the general zone is influenced by not only the local zone but also by the overall geometry of the member and the reinforcement that exists in the member. Since the engineer of record has the most complete understanding of the geometry and reinforcement within the member, it follows that the engineer of record should be responsible for the design of the general zone.
5. Myth: Post-tensioned buildings experience significantly more shortening than non-prestressed buildings.
Reality: All concrete will experience shortening. It is inherent in the curing process of the material. When concrete cures it undergoes volume change and shrinks. Contractors must control the geometry of the building by setting forms to account for the shrinking. Post-tensioned slabs experience additional elastic shortening due to prestress; however, this additional shortening is a fraction of the overall shortening of the slab. So, while post-tensioned buildings experience more shortening than non-prestressed buildings, the overall increase is insignificant.
6. Myth: Post-tensioning can’t be used in below-grade applications.
Reality: Below grade applications are structures like parking garages that are built below buildings. There is a common misconception that there is not enough room to stress the PT in a below-grade situation because of the confines of the surrounding walls. There is also the fear that the surrounding walls will result in restraint to shortening cracking. There are several strategies that can be used to achieve the benefits of post-tensioning but they require the expertise of a PT specialist. Benefits of PT below-grade include reduced cracking, enhanced durability, thinner slabs, and reduced excavation.
7. Myth: Drop panels need to be 1/6 the span in order to be used in the calculation of section properties for strength calculations.
Reality: ACI 318 code states that the size of the drop panel has to be ⅙ of the span in each direction for conventionally reinforced concrete only. This size limitation does not apply to PT slabs. The engineer has tremendous flexibility to size relatively small and efficient drop panels that are effective in shear and flexure.
8. Myth: The more post-tensioning, the better.
Reality: Post-Tensioning is not a cure-all that can compensate for sloppy design. Unlike adding more rebar to conventional reinforced concrete, more PT can have detrimental effects. Post-Tensioning is an active force on the concrete. Too much PT can create an overbalancing effect. Overbalancing usually manifests itself during construction causing deflection problems, cracking, or severe blowouts. The repair can be complicated and expensive.
9. Myth: Post-tensioning reduces material costs.
Reality: Okay, this one is true. However, the use of post-tensioning also results in many other cost savings to the owner that are often overlooked. The following is a list of additional cost-savings to the owner:
Overall building height is reduced. This can be used to add more leasable space within the same building height, it can be used to increase ceiling height, or it can be a cost savings.
Because the building height is reduced, there is a reduction in all building services that are tied to building height such as mechanical, electrical, plumbing, elevators, etc.
Because the building height is reduced, there is a savings in the cost of the building façade.
Because the building height is reduced, operating costs such as heating and cooling costs are reduced for the life of the building.
When used in below-grade applications, excavation costs are reduced.
Formwork and reshoring costs are reduced.
10. Myth: Cracks in the wedges indicate a post-tensioning system defect.
Reality: In a post-tensioning system that’s been calibrated correctly, the steel wedges that anchor the strands can be subject to cracking. What may appear to be a defect to the untrained eye is actually a design safety built into the system. Cracks indicate that the wedges are conforming more tightly and getting a better grip on the steel strands as they hold the prestress force in place. It is common to see cracks in 2-part wedges after stressing. It is less common in 3-part wedges.
Now that we’ve busted through the myths, you can confidently design and build using post-tensioning.
As you begin the planning process for your next building project consider this, and if you have any questions as you prepare, consult an expert!
EVERYTHING YOU NEED TO KNOW ABOUT BUILDING WITH CONCRETE PODIUM SLABS
With the growing demand for mixed-use buildings and the popularity of high-rise wood structures, the use of concrete podium slabs to properly support them has surged as well. If you’re considering building your next project with concrete podium slabs, here’s what you can expect.
WRITTEN BY KLINE ENGINEERS, KATHERINE FARLEY AND LAYTH HUSSEIN.
With the challenge to have all new building, developments and major renovations carbon-neutral by 2030., architects are increasingly only specifying sustainable materials. The trend has made concrete and wood appealing alternatives to steel for mid-rise and high-rise buildings.
Why do more mixed-use projects mean more concrete podium slabs?
With the growing demand for mixed-use buildings and the popularity of mid-rise wood structures, the use of concrete podium slabs to properly support them has surged as well. If you’re considering building your next project with concrete podium slabs, here’s what you can expect:
Below Ground Construction
The concrete structure supporting the podium slab can extend several levels below ground to increase site capacity and create additional service floors. Underground service levels can be used as additional parking garages, storage space, maintenance and utility, etc. This is a big advantage for projects that require off-street parking in highly condensed neighborhoods and/or add to the overall resident convenience.A higher level of quality
Concrete is stronger and stiffer than a wood base, giving your building better seismic resistance, greater fire safety, and a higher level of sound protection.Greater design flexibility
A concrete podium slab allows the designer the freedom to use a completely different floor plan between the above and below levels. Moreover, a concrete podium slab has no restrictions to support load-bearing walls from the structure above.Mixed-use areas
Concrete podium slabs can accommodate designs to create a mixed-use space at ground level such as retail shops and restaurants.
Why is post-tensioning often the best solution?
Among all types of podium design options, post-tensioning has the largest range of financial benefits from design and construction standpoints.
Shallow Members
Podiums are required to support several levels of steel/wood framing above. The inherent ability of PT (post-tensioning) to balance a portion of this load allows the design to work with a thinner concrete section compared to a conventional podium slab. These material savings can easily represent two or more inches of slab thickness reduction along with lighter concrete elements to support it.Long Spans
The column layout to support podiums can become challenging when trying to design uninterrupted parking spaces and vehicle drive isles below. Limiting deflections in these long spans is critical. PT concrete podiums excel at this feature due to their ability to balance loads. The ability of PT to help balance a portion of the dead and live load has the effect of increasing strength and minimizing deflections. PT podium slabs outperform conventional concrete slabs significantly.
Crack Control
Slabs crack when tensile stresses in the slab exceed the tensile strength of the concrete. A PT concrete podium slab provides better crack control due to the pre-compression applied to the structure.
What’s involved with creating a post-tensioned concrete podium?
Now that you know the benefits of building with a post-tensioned concrete podium, you may want to know how to go about. We partner with developers and architects that run the gamut in terms of experience - from seasoned post-tensioned concrete podium slab builders to newcomers in the field. While all engineering firms have their own processes we’ve outlined our standard procedure to give you a behind-the-scenes look at how these projects typically work.
Design development stage. We understand how critical it is to the owner/architect for the ground level to remain unchanged while proposing a column layout to support the podium slab. In the case where a column layout has already been established by the owner/architect, Kline Engineering will provide preliminary design options for the given column layout and explore relocating columns with intentions of achieving a more efficient design if necessary.
Design stage. We work and coordinate closely with the architect and build team to ensure the structural design of the podium can accommodate components such as sleeves, embedment, large openings, stairs, and elevator shafts. We thrive on establishing an open line of communication between all parties during this critical stage.
Construction stage. This is when the rubber meets the road, and this is where time critical challenges can surface. We work with the construction team to resolve these challenges quickly and efficiently so that the project is a success and ultimately our clients are more successful.
Post-tensioned concrete podiums will continue outperforming conventional concrete podiums due to their improved performance and low-cost. This framing system can bring huge value to a project.
Interested in learning more about Post Tensioning? Download our Guide.
As you begin the planning process for your next building project consider this, and if you have any questions as you prepare, consult an expert!
RULES FOR SIZING DROP PANELS IN PT FLAT SLABS
Most engineers are familiar with the limitations on the size of drop panels in two-way non-prestressed slabs.
Most engineers are familiar with the limitations on the size of drop panels in two-way non-prestressed slabs.
ACI 318-19, Section 8.2.4 describes two qualifications:
(A) Depth of the drop panel must be at least ¼ of the slab thickness away from the drop panel; and
(B) The drop panel must extend 1/6 of the span length from the center of support in each direction
It is important to note that these limitations do not apply to prestressed slabs, which allows the designer tremendous flexibility in sizing drop panels to increase negative moment capacity and reduce non-prestressed reinforcement over the columns. For example, you do not need to design large drop panels that are 1/6 of the span length in each direction in order to take advantage of the increased section for flexure.
We recommend that the depth of the drop below the slab soffit be at least 4 in., which is the nominal depth of a 2 x 4 plus ¾ in. plywood sheathing (plyform). The depth of the drop should be increased if required to increased punching shear capacity. I further recommend using a minimum drop panel size of 4 x 4 ft in plan. The size of the drop should be increased if necessary to increase flexural or punching shear capacity and fit shear reinforcement within the dimensions of the drop.
If you have any questions as you size your drop panels, consult an expert!
Reference: Bondy, K., “The Use of Drop Caps to Reduce Flexural Reinforcement in Two-Way Post-Tensioned Slabs,” FAQ No. 10, Post-Tensioning Institute, Farmington Hills, MI, March 2010, 2 pp.